Vortex Flow meter
A vortex flow meter is a type of flow measurement device that uses the principle of the vortex shedding effect to determine the flow rate of a fluid (liquid, gas, or steam) in a pipe. It is widely used in industrial applications due to its reliability, accuracy, and ability to handle a wide range of flow conditions.
All You Need to know About Vortex Flow Meter
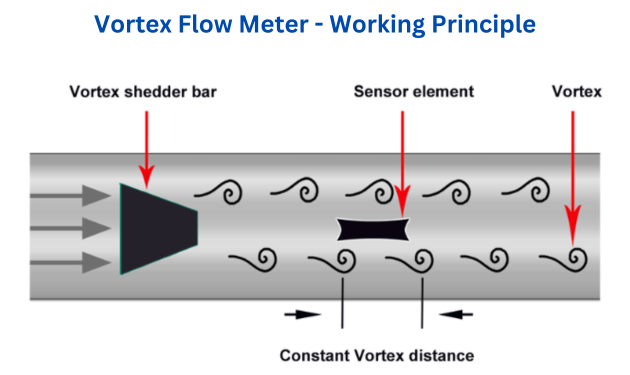
Vortex Flow Meter Principle
The Vortex Flow Meter works as follows:
Bluff Body: A non-streamlined obstruction (bluff body) is placed in the fluid flow.
Vortex Formation: As fluid passes the bluff body, alternating vortices (swirling patterns) are generated on either side, forming a “vortex street.”
Frequency Detection: A sensor (e.g., piezoelectric, capacitive) detects the frequency of these vortices.
Flow Calculation: The vortex shedding frequency is proportional to the fluid velocity. The flow rate is calculated using: Flow rate = Meter factor × Vortex frequency.
Output: The signal is converted into an electrical output for display or further processing.
This principle ensures accurate, reliable flow measurement for liquids, gases, and steam.
Advantages of Vortex Flow Meter
No Moving Parts
Durable and low maintenance.
High Accuracy
Especially at higher flow rates.
Simple Design
Easy to install and operate.
Wide Application
Can measure liquids, gases, and steam.
Vortex Flow Meter Application
- Industrial Processes: Monitoring flow rates of liquids, gases, and steam in chemical, petrochemical, and manufacturing industries.
- HVAC Systems: Measuring water or refrigerant flow in heating, ventilation, and air conditioning systems.
- Energy & Power: Steam flow measurement in power plants for boiler efficiency and energy management.
- Water & Wastewater: Flow monitoring in treatment plants, pipelines, and distribution networks.
- Oil & Gas: Measuring natural gas, crude oil, and hydrocarbon flows in pipelines and refineries.
- Food & Beverage: Ensuring precise flow control in processing and packaging lines.
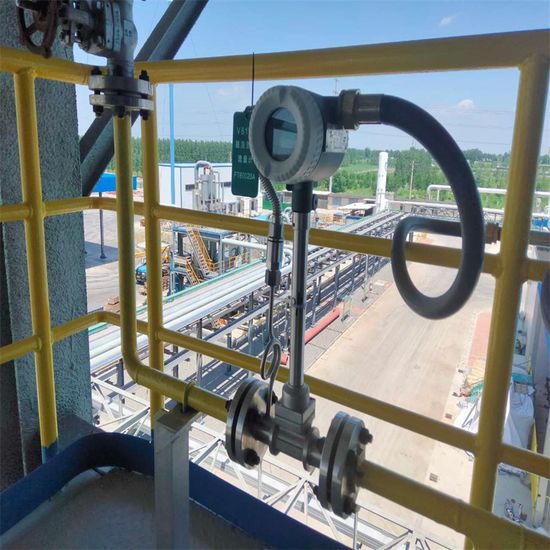
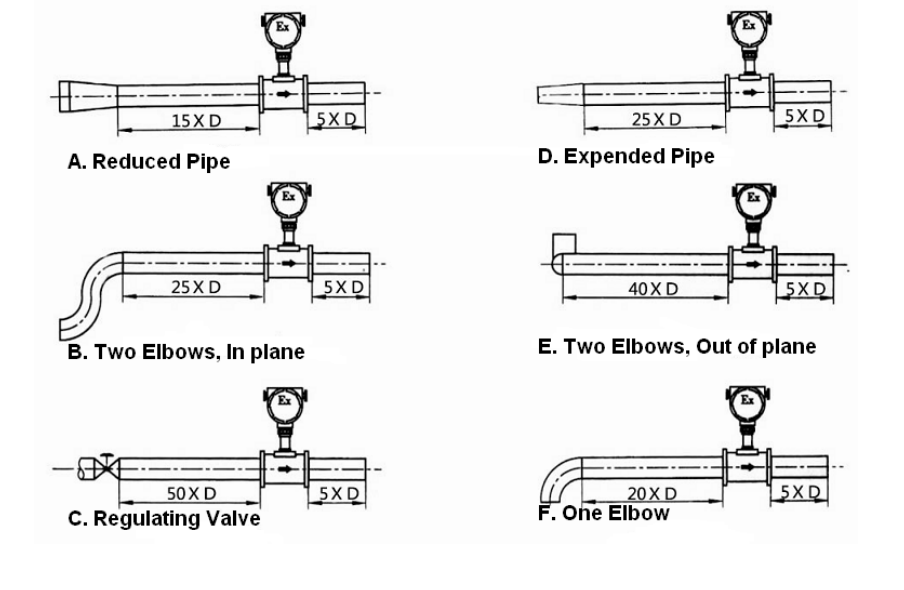
Installation Requirement
vortex flow meter upstream and downstream requirements
Required Lengths of Straight Runs
Flow altering devices such as elbows, valves, and reducers can affect accuracy. See the diagram for typical flow meter system installation.
The recommended guidelines are given to enhance accuracy and maximize performance. The distance given here are minimum requirements; double them for desired straight pipe lengths.
- Upstream: allow a minimum straight pipe length at least 10 times the internal diameter of the pipe. For example, with the 50mm pipe, there should be 500mm of straight pipe immediately upstream. The desired upstream straight pipe length is 1000mm.
- Downstream: allow a minimum straight pipe length at least 5 times the internal diameter of the pipe. For example, with the 50mm pipe, there should be 250mm of straight pipe immediately upstream. The desired upstream straight pipe length is 500mm.
Production Process
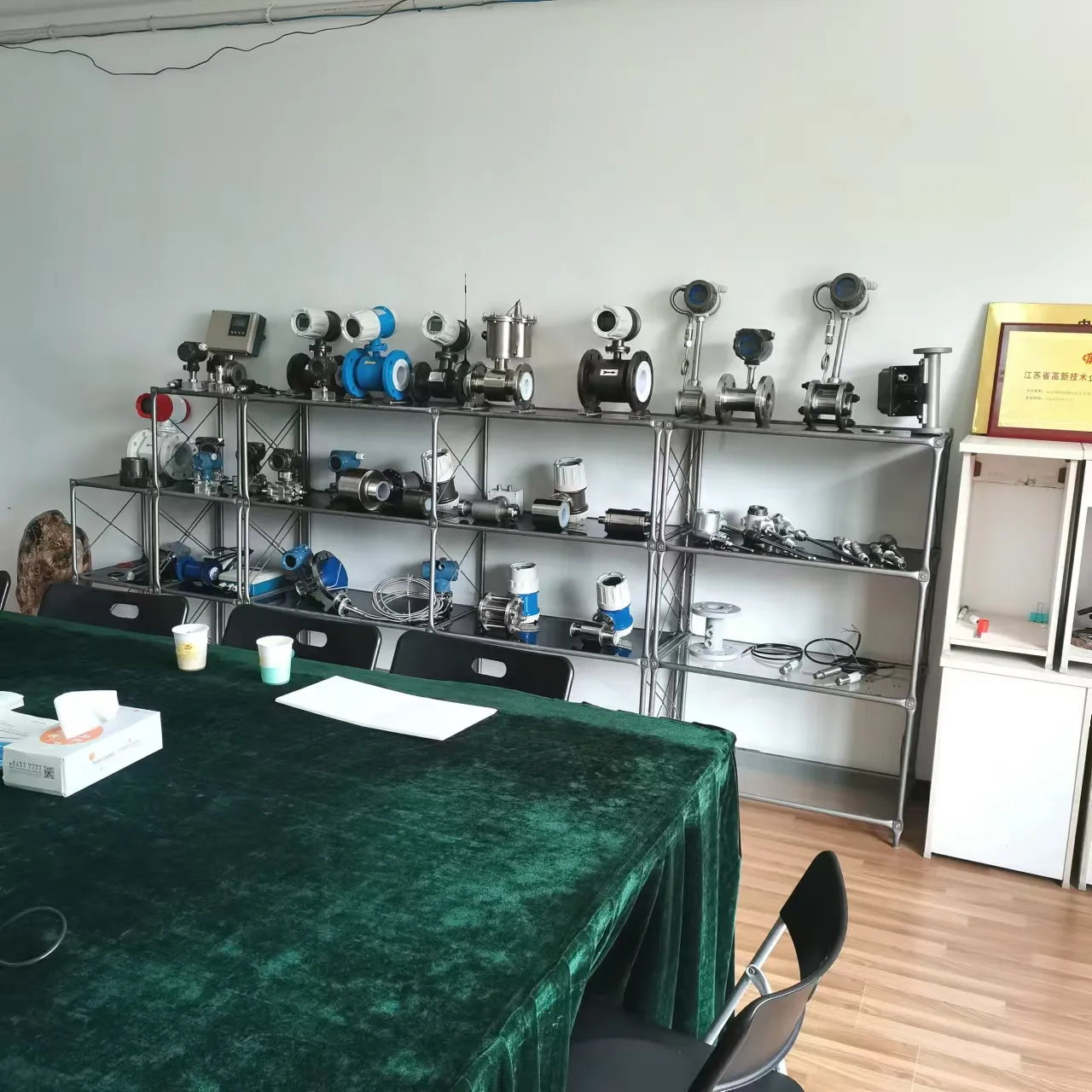
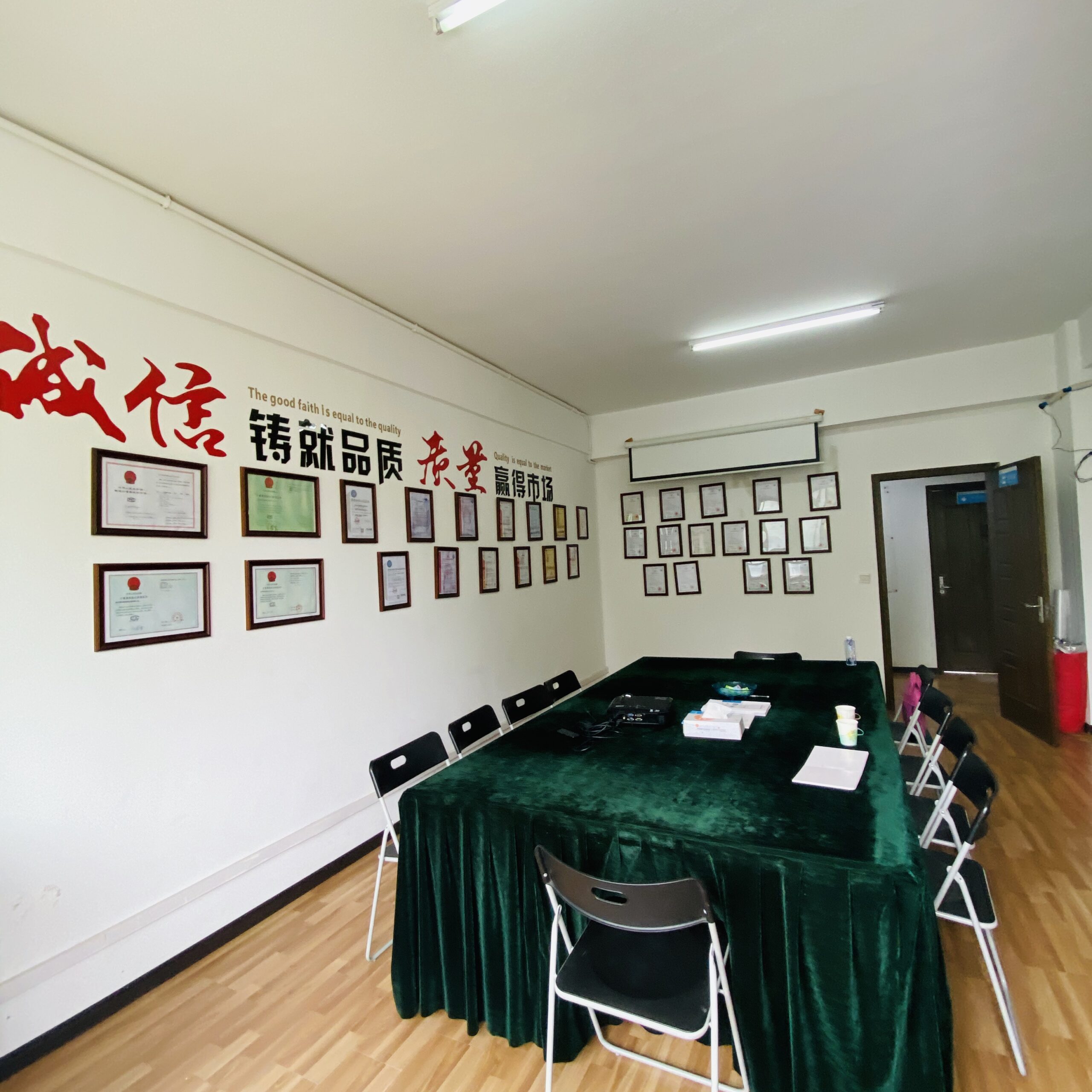
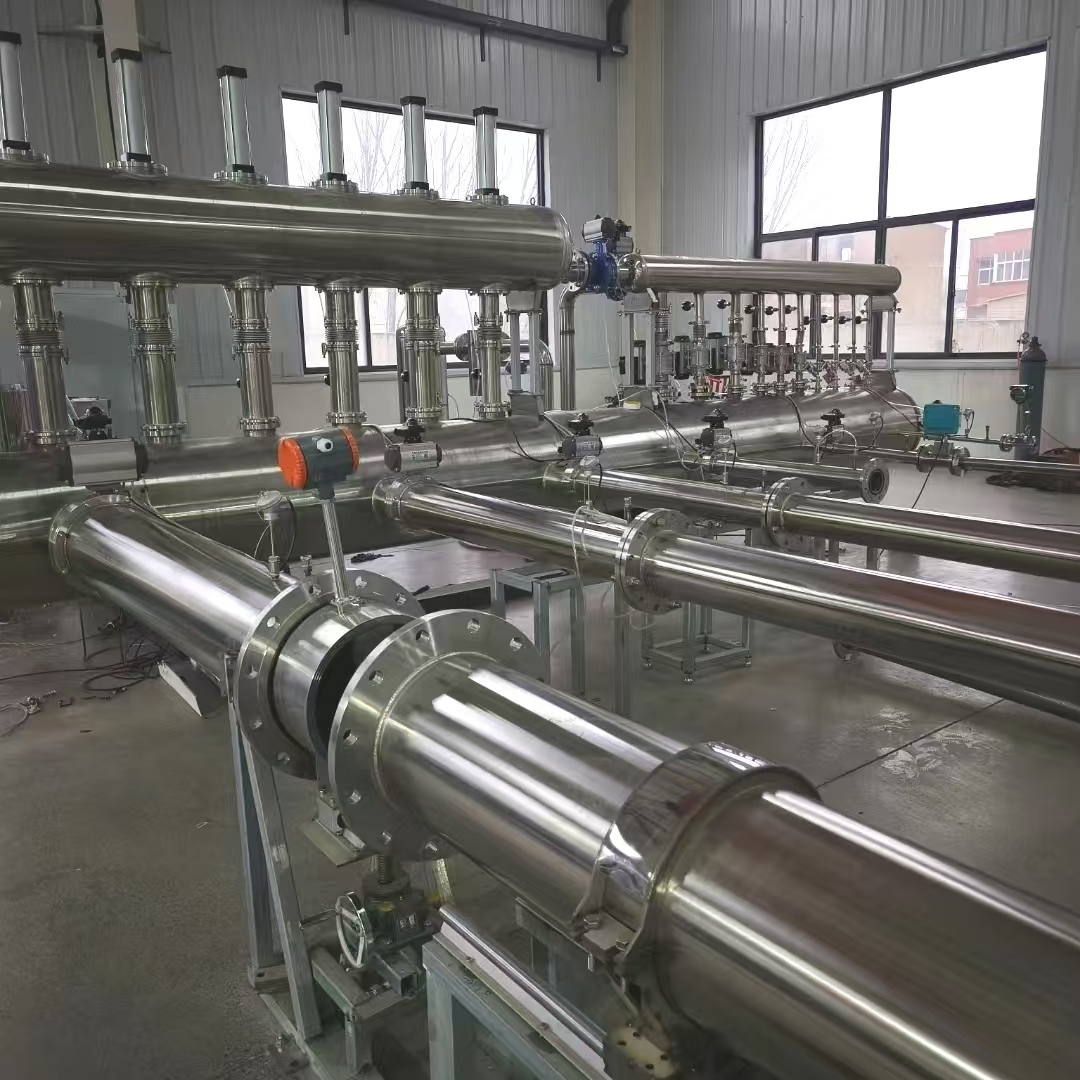
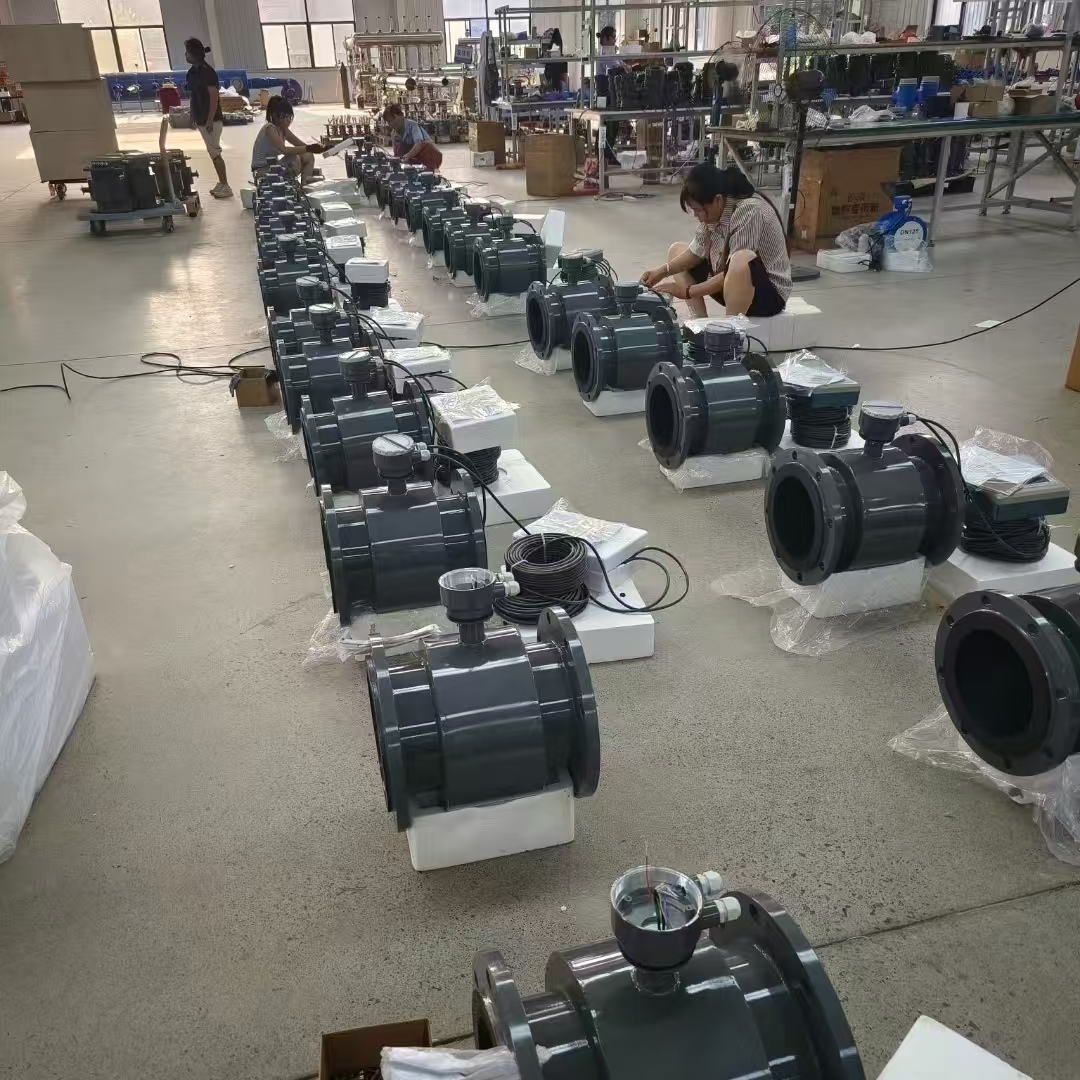
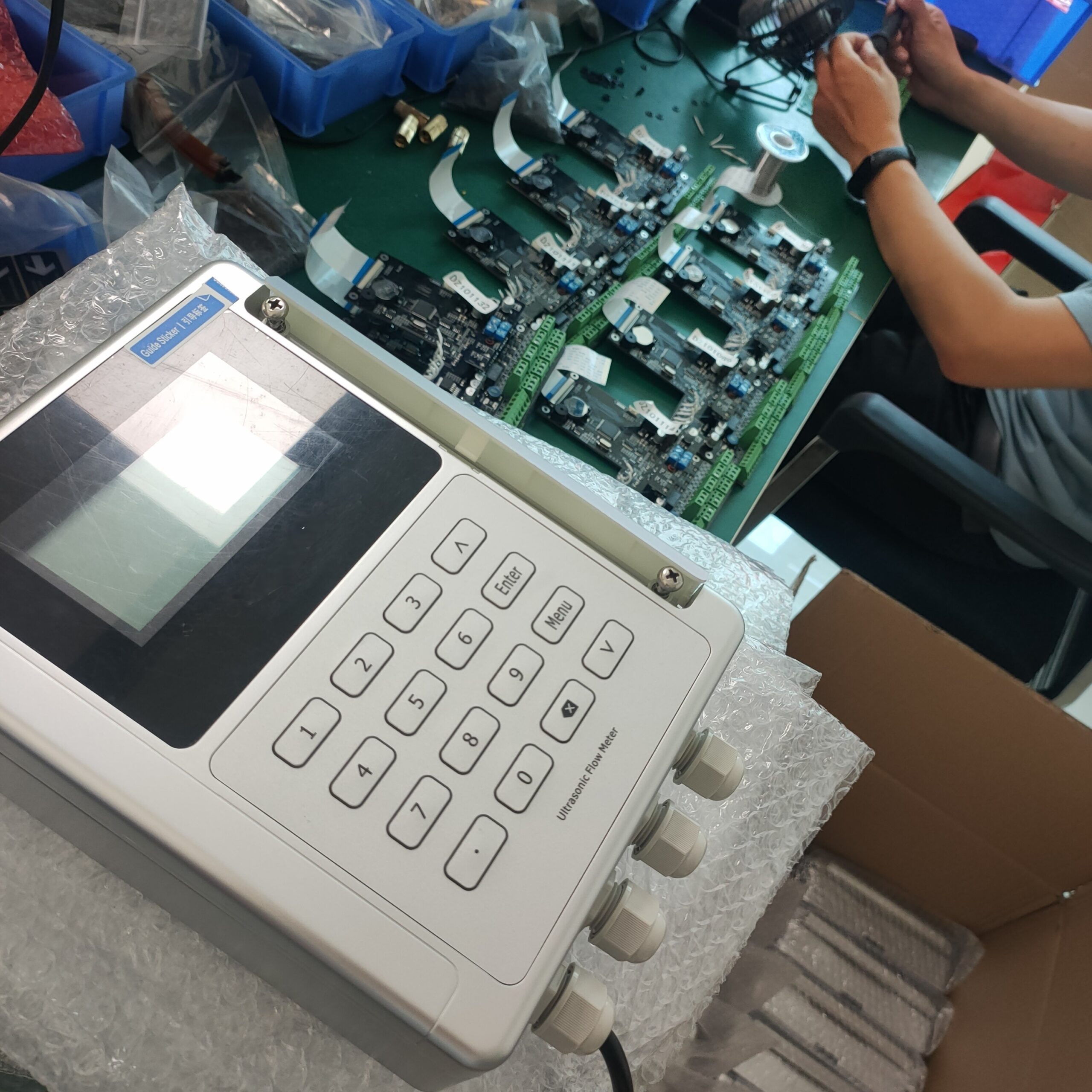
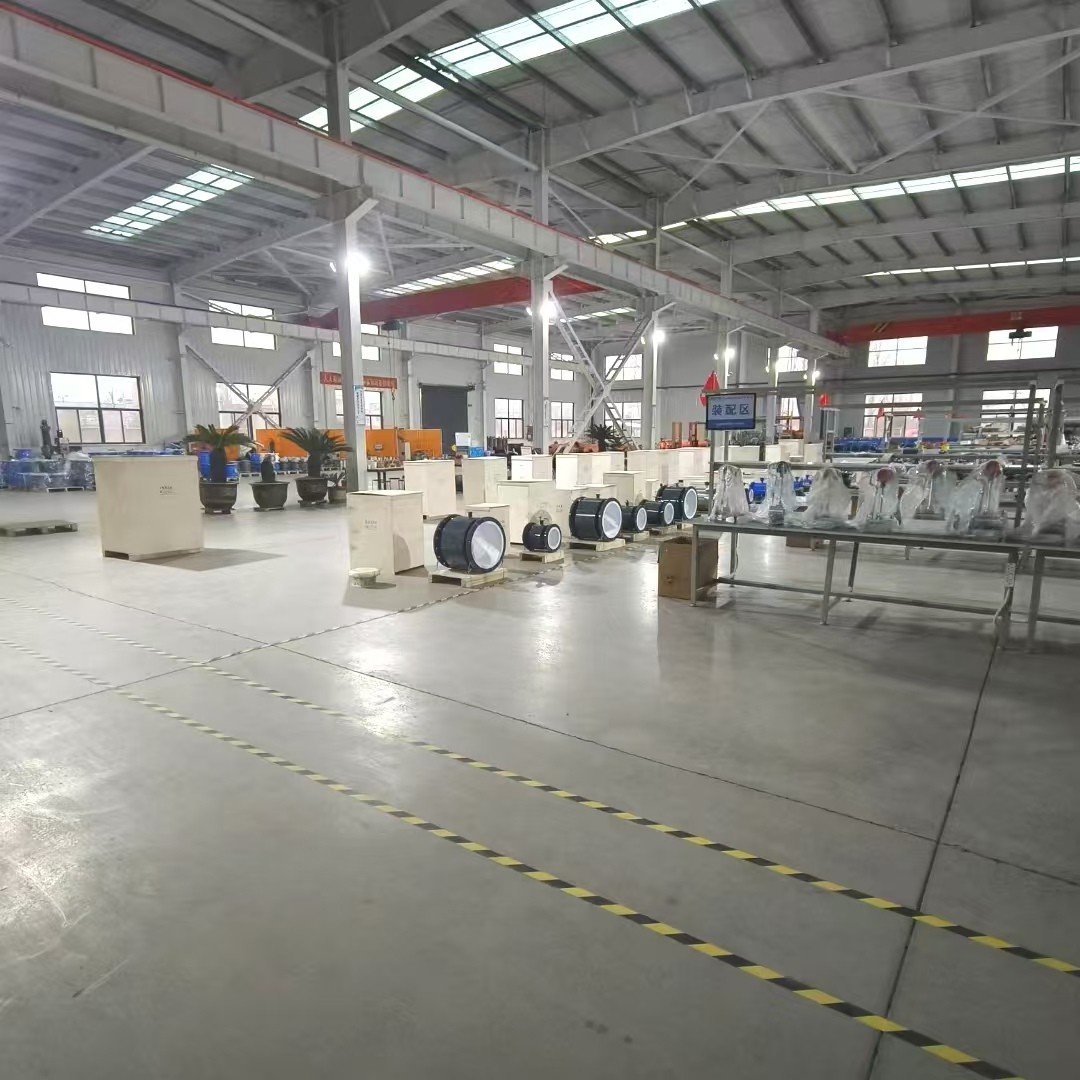
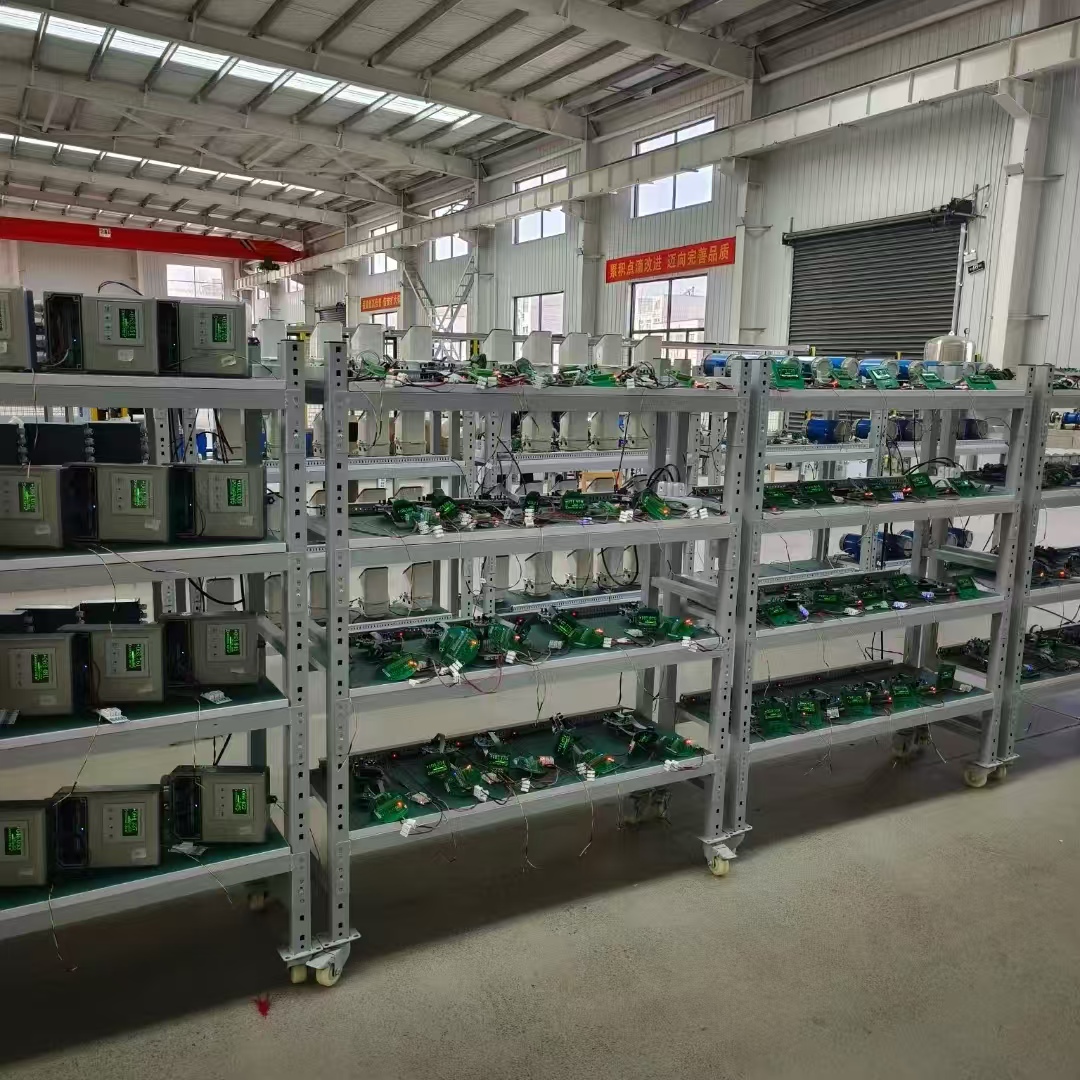
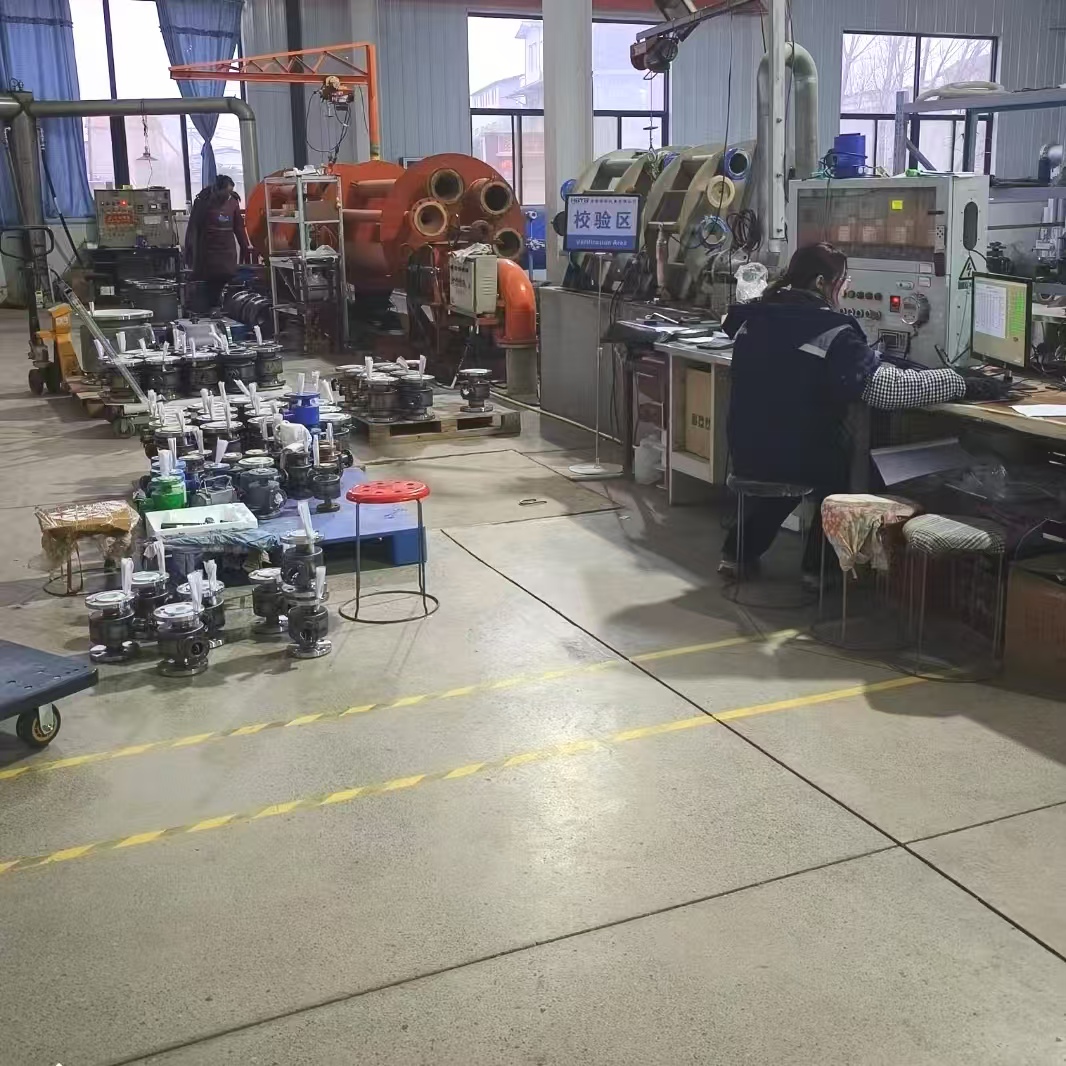